Alumina-Graphite
Stopper Rods:
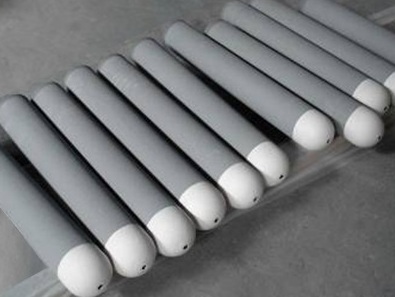
We offer ISO-statically pressed carbon bonded alumina-graphite stopper rods with enhanced composition wear bands. We also offer argon purging where necessary for the particular casting and cleanliness requirements of a shop. We have various head compositions to ensure throttling control and a clean shut-off at the end of the casting sequence, as well as a choice of designs with rigging supplied with the stopper as required.
Graphic Illustration:
- Multiple designs for attaching the rigging.
- Ceramic glaze coating to prevent external oxidation. High temperature glaze coatings are available for extreme preheat conditions.
- Zr-based slag zone composition to ensure greater resistance to slag corrosion.
- High quality AL-C materials having high corrosion and thermal shock resistance.
- Porous plug to prevent steel from entering the stopper.
- Spinel head materials having exceptional resistance to slag corrosion.
- Mg-C head materials having good slag corrosion resistance when processing steel with Ca.
- High quality Zr-based materials to ensure good corrosion resistance of the head.
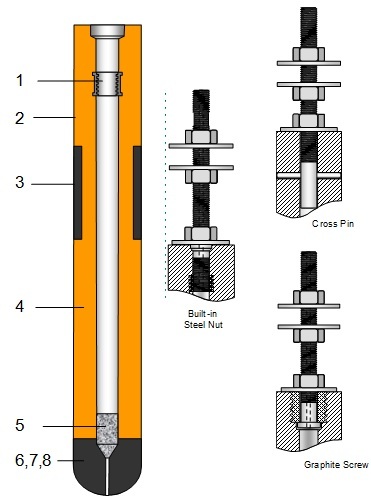
Ladle Shrouds
ISO-statically pressed carbon bonded alumina-graphite ladle shrouds, with enhanced composition wear bands and argon channels as necessary for the particular casting and cleanliness requirements of a shop are available. Preheat is not required as the shrouds are free of thermal shock characteristics. A variety of gasket designs and materials are also available for easy disconnect between heats.
Graphic Illustration:
- Multiple argon injection designs engineered for customer requirements.
- Precision steel components for protection of the ceramic body.
- Enhanced bowl composition for greater protection during lancing.
- Ceramic glaze coating to prevent external oxidation.
- Ceramic fiber to prevent heat loss during casting.
- High quality Al-C materials having high corrosion and thermal shock resistance.
- High quality composites to provide enhanced corrosion resistance at the slag line.
- Non-graphite based materials to meet the requirements of producing low carbon steel, silicon steel and high purity steel.
- Reverse taper and bell designs for the prevention of "blow-back" during submerged openings.
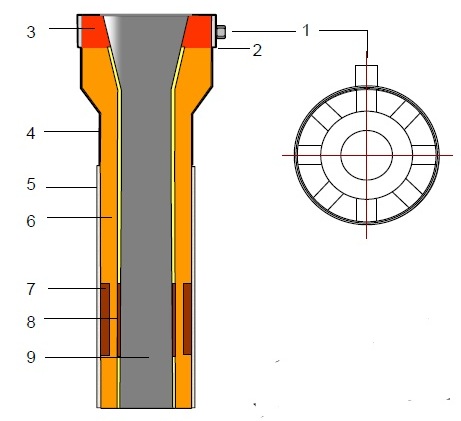
Alumina-Graphite SEN -SES
ISO-statically pressed carbon bonded alumina-graphite SEN (sub-entry nozzles) and SES (sub-entry shrouds) with enhanced composition wear bands, argon channels and anti-clogging inner layers as necessary for the particular casting and cleanliness requirements of a shop.
Graphic Illustration:
- Multiple argon injection designs engineered for customer requirements.
- Precision steel components for protection of the ceramic body.
- Enhanced bowl and seat compositions for an improved seal.
- Ceramic glaze coating to prevent oxidation during preheat. High temperature glaze coatings available for extreme preheat conditions.
- Ceramic fiber to prevent heat loss during preheat and casting.
- 2High quality Al-C materials having high corrosion and thermal shock resistance including compositions with special antioxidants for high O2 steels.
- High quality composites to provide enhanced corrosion resistance at the slag line.
- Non-graphite based materials to meet the requirements of producing low carbon steel, silicon steel and high purity steel.
- Anti-clogging inner layers and Slit SEN technology.
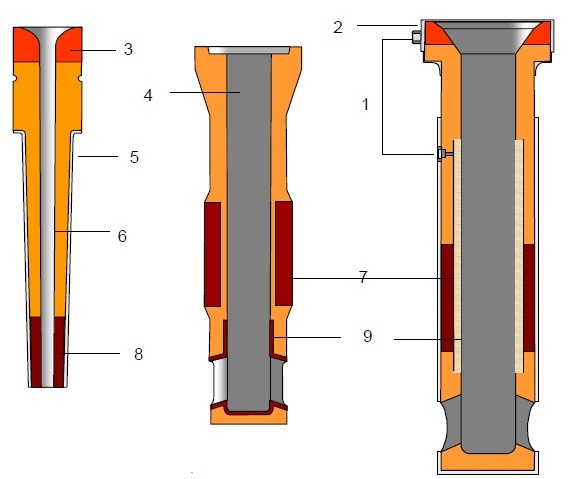
Tundish Upper Nozzles
Graphic Illustration:
- Al-C body materials having high corrosion and thermal shock resistance.
- Enhanced Al-C materials for the bowl structure having high corrosion resistance.
- Spinel compositions for the bowl structure to assure better adoption of the stopper including exceptional good resistance to slag corrosion.
- Mg-based compositions for the bowl structure having good corrosion resistance to slag containing Ca.
- Compositions to prevent Al2O3 adhesion inside the nozzle.
- Argon injection designs to prevent air ingress.
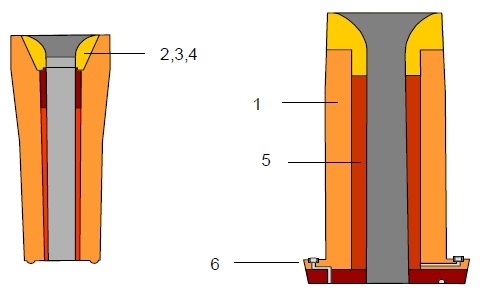
Alumina-Graphite Quick Change and Thin Slab SEN1
ISO-statically pressed carbon bonded alumina-graphite SEN (sub-entry nozzles) and SES (sub-entry shrouds) with enhanced composition wear bands, argon channels and anti-clogging inner layers as necessary for the particular casting and cleanliness requirements of a shop.
Graphic Illustration:
- Multiple argon injection designs engineered for customer requirements.
- Precision steel components for protection of the ceramic body.
- Enhanced bowl and seat compositions for an improved seal.
- Ceramic glaze coating to prevent oxidation during preheat. High temperature glaze coatings available for extreme preheat conditions.
- Ceramic fiber to prevent heat loss during preheat and casting.
- High quality Al-C materials having high corrosion and thermal shock resistance including compositions with special antioxidants for high O2 steels.
- High quality composites to provide enhanced corrosion resistance at the slag line.
- Non-graphite based materials to meet the requirements of producing low carbon steel, silicon steel and high purity steel.
- Anti-clogging inner layers and Slit SEN technology.
- Composite sliding surface materials to ensure sealing and fast change.
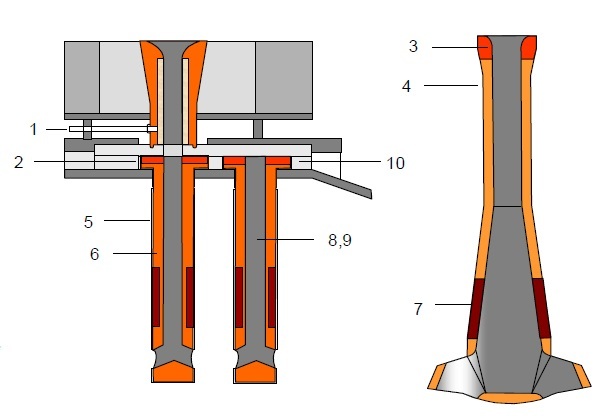